Membrane Bioreactors (MBR)
Membrane Bioreactors (MBRs) combine biological filtration with membrane filtration. They effectively reduce COD, BOD, nitrogen, and phosphorus.
Membrane Bioreactors Explained
An MBR, or membrane bioreactor, combines the biological degradation of a bioreactor with membrane filtration. This dual approach makes MBRs highly effective for treating both industrial and municipal wastewater. In MBR systems, wastewater undergoes treatment in a bioreactor where microorganisms degrade pollutants. The core component, the MBR membrane bioreactor unit, immerses directly in the bioreactor, filtering and separating solids from the clean water. The result is a high-quality effluent ideal for reuse or safe environmental discharge
MBRs stand out for their efficiency in treating high-strength wastewaters and their smaller footprint compared to traditional systems. They are ideal for places where space is limited or where environmental regulations require high-quality effluent. Their automated nature also makes MBRs a low-maintenance, user-friendly choice for effective wastewater management.
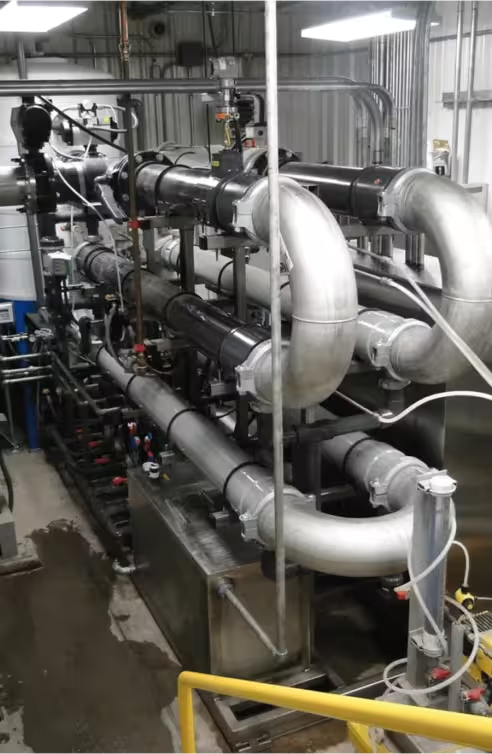
Case Studies
How do MBR systems work?
Membrane Bioreactors (MBRs) are an advanced solution in wastewater treatment, combining conventional biological treatment processes with membrane filtration. Here's a step-by-step breakdown of how they work:
Biological Treatment:
Wastewater first enters a bioreactor where it undergoes biological treatment. The reactor has a cell culture-like environment. In this stage, organic matter in the wastewater is degraded by microorganisms. This process is similar to what happens in a conventional activated sludge system, but it occurs in the same tank where the membrane modules are installed.
Membrane Filtration:
After the biological degradation, the next step is filtration through membranes. MBR systems typically use ultrafiltration or microfiltration membranes, which are often hollow fiber, or flat sheet filters. These membranes are submerged in the bioreactor or placed in a separate tank. They have tiny pores that allow water to pass through while retaining suspended solids, bacteria, and viruses.
Aeration:
Aeration is a crucial part of the MBR process. Air is bubbled through the bioreactor not only to provide oxygen to the microorganisms (which aids in the biological treatment process) but also to help keep the membranes clean. The air helps to prevent the accumulation of solids on the membrane surfaces, a phenomenon known as fouling.
Permeate Extraction:
The clean water that passes through the membrane is called permeate. This water is typically of high quality and can be reused in many applications or discharged to the environment, adhering to stringent discharge standards.
Sludge Management:
The solids retained by the membrane are periodically removed from the system. This waste activated sludge can then be further processed or disposed of according to local regulations.
MBRs are particularly effective because they can achieve a high level of pollutant removal, including nutrients like nitrogen and phosphorus. They are also space-efficient and can be scaled up or down to suit different treatment capacities, making them a versatile option for both municipal and industrial wastewater treatment.
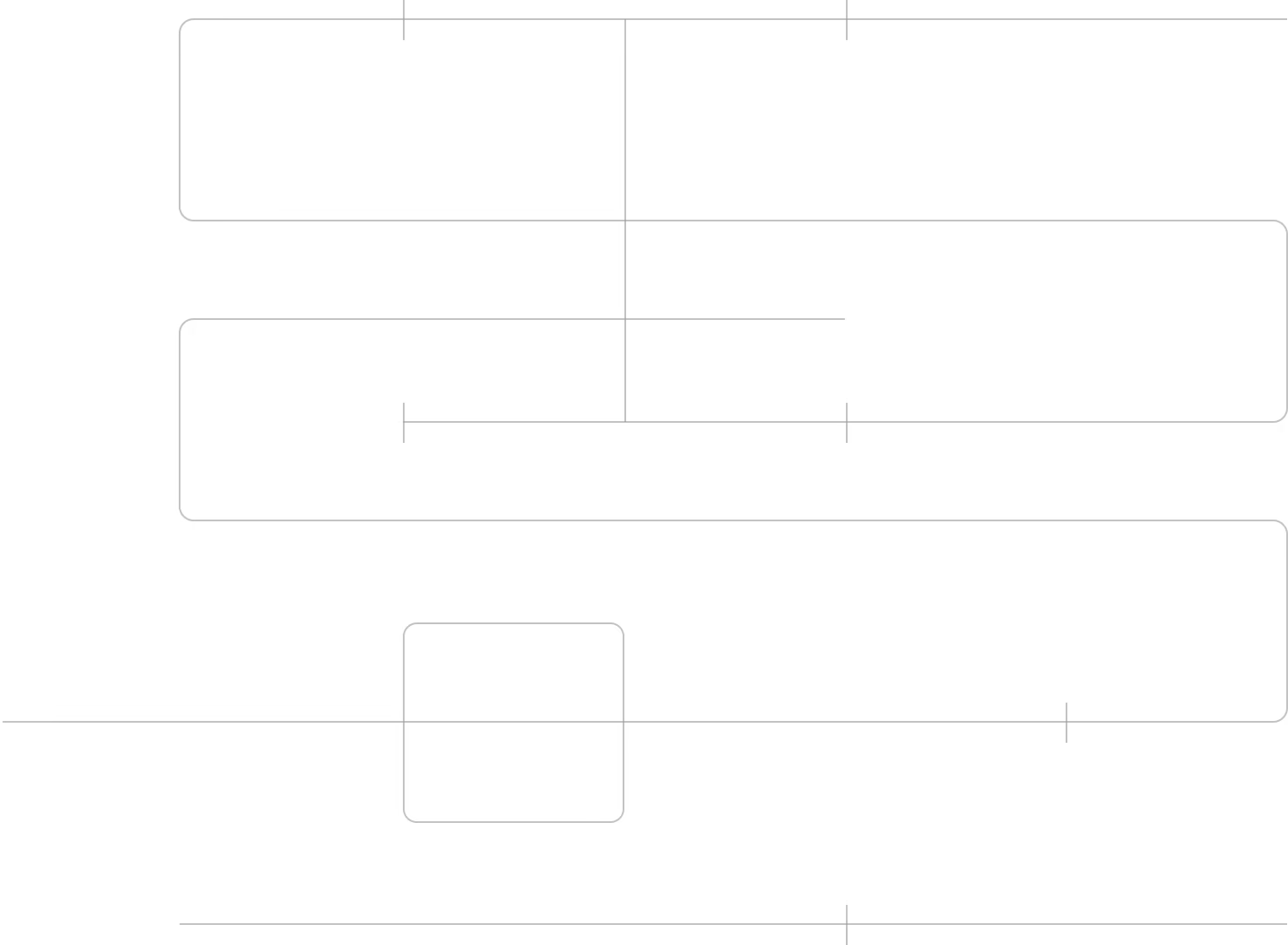
Why Choose bioprocessH2O for MBRs?
When it comes to implementing Membrane Bioreactor (MBR) technology, choosing the right partner is crucial. At bioprocessH2O, we leverage our deep expertise in process development and operating systems to deliver customized MBR solutions:
Expertise and Experience:
With years of industry experience, bioprocessH2O has a proven track record of delivering high-quality MBR systems. Our team of experts understands the intricacies of MBR technology and is adept at designing and implementing systems that meet the specific needs of each client.
Customized Solutions:
We recognize that each wastewater treatment challenge is unique. Our approach is to provide customized MBR solutions tailored to the specific requirements of your project, whether it’s for municipal, industrial, or specialized applications.
Advanced Technology:
At bioprocessH2O, we utilize the latest in MBR technology. Our systems are designed for optimal performance, efficiency, and reliability. We continuously innovate to incorporate the most advanced features in our systems.
Quality and Compliance:
Every MBR system we provide is built to the highest quality standards, ensuring robust performance and longevity. We also ensure that our systems meet or exceed all regulatory compliance standards for wastewater treatment.
Customer-Centric Service:
Our commitment to our clients goes beyond the installation of the system. We offer comprehensive support, including maintenance, training, and troubleshooting, to ensure your MBR system operates at peak efficiency.
Environmental Responsibility:
As a company, we are committed to sustainability. Our MBR systems are designed not just for effective wastewater treatment, but also for minimal environmental impact, supporting your sustainability goals.
Cost-Effectiveness:
We understand the importance of budget considerations. Our MBR solutions are not only effective but also cost-efficient, providing long-term savings in operation and maintenance.
Choosing bioprocessH2O for your MBR needs means partnering with a leader in wastewater treatment technology. We are dedicated to providing you with a system that delivers exceptional performance, meets your specific needs, and supports your environmental and financial goals.
.avif)
Superior Water Quality
Compact Footprint
High Operational Efficiency
Low Sludge Yield
Flexibility and Scalability
Automated Operation
Enhanced Nutrient Removal
Enhanced Nutrient Removal
Energy Efficiency
Adaptability
Additional Benefits
- Superior Water Quality: Our MBRs deliver exceptionally high-quality effluent, suitable for a variety of reuse applications, surpassing conventional treatment methods.
- Advanced Nutrient Removal: Efficiently removes nitrogen and phosphorus, making it ideal for areas with strict effluent quality regulations.
- Automated Control System: Equipped with an advanced automated control system for optimized performance with minimal manual intervention.
- Flexibility in Treatment Capacity: MBRs are adaptable to both low and high-capacity treatment needs, making them suitable for a wide range of applications.
- Resistant to Upset Conditions: Our MBR systems are robust and can handle shock loads better than traditional systems, ensuring consistent performance.
- Reduced Sludge Production: MBRs produce less sludge compared to conventional processes, lowering handling and disposal costs.
- Space-Saving Design: The compact design of our MBRs requires significantly less space than traditional wastewater treatment setups.
- Eco-Friendly Operation: Lowers the ecological footprint of wastewater treatment by reducing energy and chemical use.
- Streamlined Installation and Commissioning: Our team ensures a smooth and efficient installation process, with comprehensive support from start to finish.
- Long-Term Partner in Wastewater Management: We don’t just provide systems; we offer ongoing support and expertise to ensure your MBR solution continues to meet your needs.
Transform Your Wastewater Treatment with MBR Technology
Contact bioprocessH2O to learn how our MBR systems can revolutionize your wastewater treatment process. Our team is ready to provide you with a tailored, efficient, and sustainable solution.
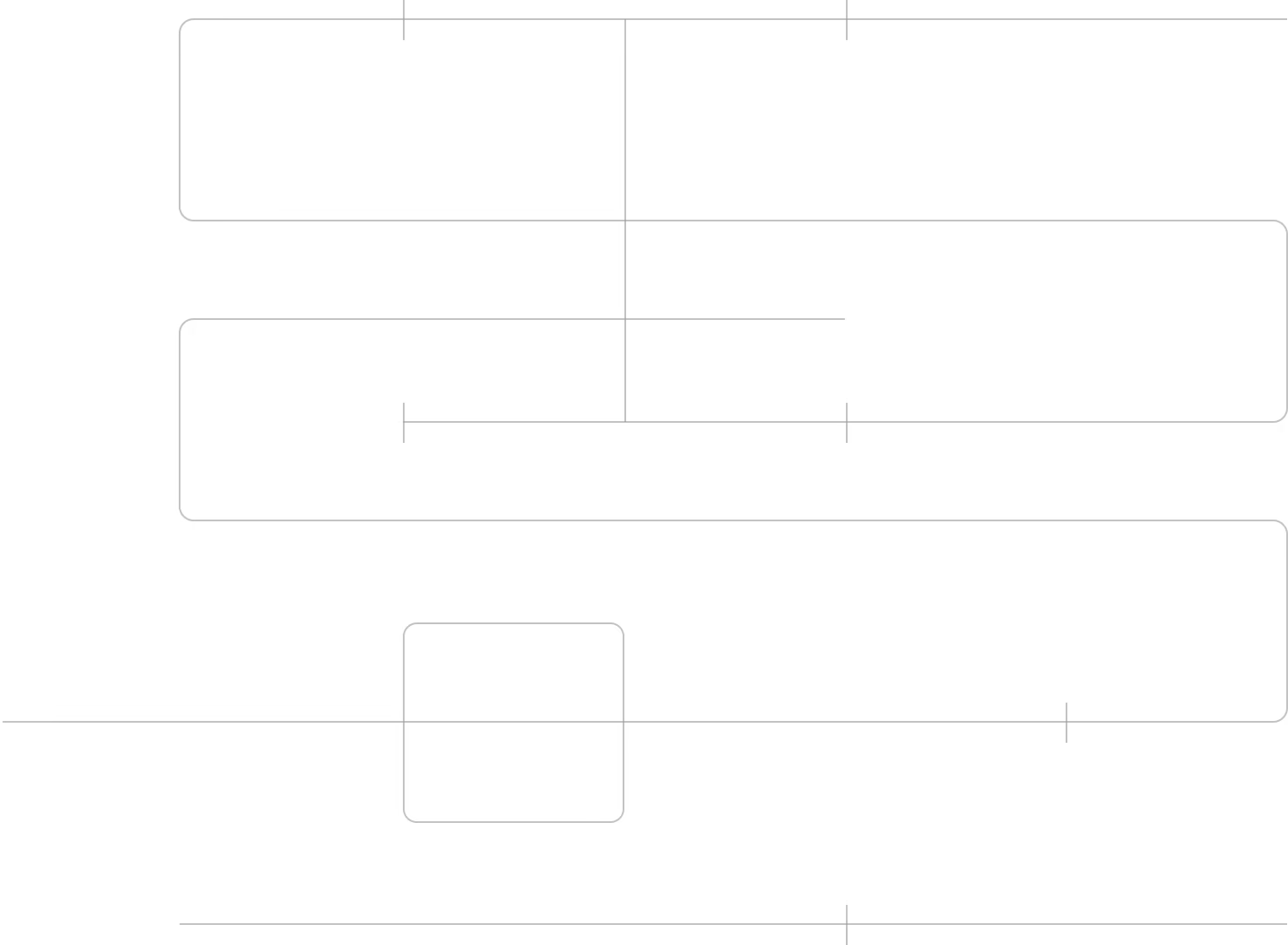